Welcome to CT State Community College Gateway
Gateway Receives Award of Merit from the Connecticut Green Building Council
Wednesday, June 19, 2013
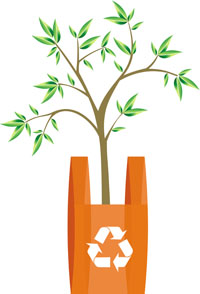
On June 20, 2013, Gateway Community College was presented with an Award of Merit from the Connecticut Green Building Council. This tremendous achievement recognizes Gateway’s continuous investment in Connecticut’s green community and what the campus has accomplished in terms of energy efficiency and sustainable building practices.
The Award of Merit comes just months after Gateway's achievement of the Leadership in Energy and Environmental Design (LEED®) Gold certification from the U.S. Green Building Council. The campus received the certification after less than a year in operation. The LEED Green Building Rating System™ is a voluntary, consensus-based standard to support and certify successful green building design, construction and operations.
The campus, which was designed by Perkins+Will, is the largest public project in Connecticut — and the largest project on any college campus in the state. It has more than 50 LEED features:
Recycled Building Materials: Almost 20 percent of the materials used to build Gateway’s new downtown campus contain recycled material. That includes almost every “finish” — interior items like tiles, drywall, ceiling panels and rubber flooring — along with most of the steel used in construction. There are two kinds of recycled content: post-consumer, like the items we put out on our curbs, and pre-consumer. The latter is anything that never reached its intended end user and usually originates from manufacturers that send unused material back to its producer. The main post-consumer recycled material used in construction was the structural steel. Today, when buildings are torn down, the steel is usually recovered and sent to a foundry for recycling. Drywall was the main pre-consumer recycled item used on the campus.
Bicycle storage and changing rooms: The new campus has 112 bike racks in its parking garage and 12 showers within locker rooms located in the North and South Buildings that are available to bicycling commuters.
Brownfield and Urban Redevelopment: A brownfield is property where expansion, redevelopment, or reuse may be complicated by the presence or potential presence of a hazardous substance, pollutant, or contaminant. The site of Gateway’s new downtown campus was a brownfield. If a construction site redevelops a brownfield, as part of the process, it must remediate contamination on site, thereby reducing the number of brownfields that exist. The construction site is made up of two parcels, one located north of the other, on 3.7 acres that formerly were home to a Macy’s and Edw. Malley Co. department store at 20 Church Street. Dimeo Construction Company, the project’s construction manager, managed the brownfield remediation with the state Department of Construction Services, which commenced in December 2009. Gateway also contributes positively to the environment as an urban redevelopment, leaving undeveloped urban property as is.
Campus-Wide Recycling Program: Gateway’s new downtown campus features single stream recycling for items such as plastic, cans, paper, cardboard, metal and glass. Bins are located on every floor, as well as in the Community Center, Cafeteria, Library and Learning Commons, Student Lounge, Early Learning Center, outdoor garden, parking garage, engineering shops, culinary arts kitchen and other spaces. The bins will be collected daily and brought to a designated area to store these recyclables until they can be recycled.
Construction Pollution Control: Dimeo Construction Co. dampened dirt on the construction site during dry months to keep dust from accumulating nearby, installed fabric silt barriers under storm water grates around the perimeter of the site to ensure site materials stay out of run-off, and created “wheel wash stations” at all the gates to clean dirt off vehicles’ tires. The stations consist of “tracking pads” of stones that help break up dirt and mud before a vehicle leaves the site. Dimeo also performed regular maintenance of pollution prevention tools and provided regular photographs to document that maintenance.
Construction Waste Recycled: Some estimates suggest more than 20 percent of the United States’ total waste stream is attributable to construction and demolition (C&D) debris. Dimeo Construction Co. diverted more than 75 percent of all the waste generated on the construction site for recycling, sending it to Murphy Road Recycling on Wheeler Street in New Haven, a C&D debris transfer station where all dry wall, metals, masonry debris, wood, paper and cardboard were removed and sent to several locations for recycling. Diverting the waste not only helps extend the life of landfills, but it also helps address global warming by reducing the use of disposal facilities and their related environmental issues and offsetting the need to extract and consume virgin resources.
Community Connectivity and Density Development: Gateway’s new campus is built on a previously developed site, so it protects greenfields and preserves habitat while utilizing existing infrastructure. Additionally, the campus is located within a half-mile of many basic services such as restaurants, which reduces vehicular use by encouraging pedestrian access instead.
Designated parking for carpools/vanpools, low-emitting or fuel-efficient vehicles: The new campus has designated parking for carpools/vanpools and low-emitting or fuel-efficient vehicles (the latter is defined as vehicles that get 35 mpg or higher).
Easy access to public transportation: The greater the portion of the GCC community that uses mass transit, the lower the emissions from commuters and demand for fossil fuels. GCC’s new downtown campus is within a half-mile of New Haven’s train station, creating pedestrian access to Metro-North Railroad and Amtrak, and is within a quarter mile of multiple bus stops.
Forestry-Friendly Wood Products: More than 85 percent of the wood products used in Gateway’s new downtown campus are certified as forestry-friendly by the Forest Stewardship Council (FSC), defined as operations that use responsible harvesting methods and replanting strategies. Almost 100 percent of the campus’ millwork, cabinets and case work, is FSC-certified, and about 80 percent of its wood doors are, too.
Green Education Program: Gateway is very cognizant of its role as an innovator among Connecticut state colleges, and takes its role of sustainability and environmental responsibility seriously, as exemplified by the construction of its new downtown campus designed to be LEED Gold-certified. As part of that role, Gateway is enacting a “green” education program that uses signage to inform and educate the public about its campus’ LEED features and will offer LEED tours for further educational outreach.
Green Housekeeping: Gateway’s new downtown campus features “green” housekeeping, a program designed to reduce the exposure of the college community and maintenance staff to potentially hazardous chemical contaminants that may adversely impact air quality, individuals’ health and the environment. The program involves the use of substitute chemicals and the selection of cleaning processes that improve the health of a building.
Green Label Carpeting: All carpet and carpet backing used in Gateway’s new downtown campus are certified through The Carpet and Rug Institute’s Green Label Program, which tests carpet, cushions and adhesives to help users identify products with very low emissions of volatile organic compounds (VOCs). VOCs are emitted as gases and may have short- and long-term adverse health effects.
Heat Recovery Units: Gateway’s new campus has heat recovery units that recycle the heat in the ventilation system’s outgoing air to warm up the fresh air coming in during winter months.
Ice Storage to Aid Air Conditioning: Gateway’s new downtown campus has ice storage tanks in the lower level of the North Building that help reduce costs associated with air conditioning by producing ice in the tanks at night when electrical rates are lower and using that ice to produce chilled water and cool the air in the building during the more expensive peak daytime hours.
Indoor Air Quality Management: When a building is being built, there are many things that can contribute to lowering the quality of the air inside, primarily dust and the “off-gassing” of a variety of volatile organic compounds (VOCs) during construction. VOCs are emitted as gases from certain solids or liquids, including things like paint, glue, sealant, even carpet and other construction materials, some of which may have short- and long-term adverse health effects. Concentrations of many VOCs are consistently higher indoors, sometimes up to 10 times higher, than outdoors. Due to the large amounts of dust and VOCs, the U.S. Green Building Council included requirements for construction indoor air quality (IAQ) management plans, both during construction and before occupancy, as part of its LEED certification process. The IAQ management plan for the downtown campus during construction laid out how workers reduced or mitigated the effects of dust and VOCs. For instance, all duct work on the site was covered to prevent dust from getting into it. Anytime a product that can emit VOCs was not being used, it was required to be covered and stored in a safe manner. There also is an IAQ management plan for campus after construction is completed, but before occupancy. Workers turn on all the venting and air handling units and run them with the windows open for an amount of time dictated by the square footage to allow the entire building to “out-gas” any remaining VOCs. Smoking was prohibited on the construction site or in the buildings at any time during construction and after occupancy.
Light Control Systems: Gateway’s new downtown campus has sophisticated light-control systems that provide at least 90 percent of its occupants with individual controllability. All classrooms have task lighting controls at the instructor’s station and shades to control daylight. And all conference and multi-purpose rooms also have combined lighting controls that include daylight sensors that shut off electrical lighting when natural daylight provides sufficient illumination levels, and occupant motion detectors to turn off lights when there is no one in the area.
Low VOC Paint, Adhesives, Sealants, Composite Wood: There are many materials used in building construction that emit volatile organic compounds (VOCs), gases that may have short- or long-term adverse health effects. The new campus includes the use of paint, adhesives and sealants that emit VOC levels within healthful limits set by the U.S. Green Building Council. Limiting these levels at the outset is especially important because concentrations of many VOCs are consistently higher indoors, sometimes up to 10 times higher, than outdoors. Adhesives and sealants include things like carpet glue and caulking. All interior paints in the buildings meet USGBC VOC guidelines, which vary depending on the specific type of paint. All composite wood used in the project, which includes all of the cabinetry, does not contain urea-formaldehyde, a resin typically used in pressed wood products that can be odorous, irritating and harmful to the comfort and well-being of installers and occupants.
Naturally Lit Atrium: One of the showcase areas of Gateway’s new downtown campus is its naturally lit, light-filled linear atrium, which features a glass ceiling and serves as an “internal street” and public meeting space for the college community. It features stadium seating that can be used for studying or informal and formal gatherings, and the President’s Learning Wall with inspirational messages.
No Smoking Policy: As with all state buildings, smoking is prohibited in Gateway’s new downtown campus and designated smoking areas are at least 25 feet away from any entry outdoor air intake vent and windows.
Optimizing Energy Performance: Gateway’s new campus is designed to use 30 percent less energy when compared with a baseline campus by optimizing energy performance to reduce the environmental and economic impacts associated with excessive energy use. It achieves this goal in a variety of ways. Daylight and occupant sensors, and reduced lighting power densities reduce electric lighting usage. Heat recovery units recycle the heat in the ventilation system’s outgoing air to warm up the fresh air coming in during winter months. Ice storage tanks help reduce costs associated with air conditioning by producing ice in the tanks at night when electric rates are lower and using that ice to produce chilled water and cool the air in the building during the more expensive peak daytime hours. Renewable energy systems produce enough power on-site to offset at least 3 percent of the campus’ total energy demand.
Outdoor Garden: Gateway’s new downtown campus features an outdoor garden outside the Community Center in the North Building. In addition to featuring water-efficient landscaping, the garden also helps offset the urban “heat island” effect by assisting in the reflection of heat.
Photovoltaic Trellis: The new campus uses two forms of solar energy. There are solar panels on the North Building to heat hot water and photovoltaic panels along the top of the entire Atrium section of the complex. Both provide the campus with self-generated energy that reduces utility costs. There are more than 300 195-watt photovoltaic panels that generate electricity that is stored in two 30-kilowatt AC inverters that feed the electricity back into the building.
Reflective “Cool” Roof: As cities are developed, buildings, roads and other infrastructure replaces open land and plant life, making areas impermeable and dry and forming an “island” of higher temperatures. This “heat island” effect causes both the atmosphere and surfaces to be noticeably warmer than nearby rural counterparts. As a result, new urban construction can add to peak summertime energy demand, related air conditioning costs, air pollution and greenhouse gas emissions. LEED includes design credits to incentivize offsetting this effect in two ways: on the roof and on all sidewalks and other hardscape surfaces. The new campus helps reduce the heat island effect in New Haven because its main roof is made of light colored material that is designed to reflect the sun’s rays rather than absorb them as a typical black roof would.
Regional Materials: The shorter the distance between a construction site and the locations where the construction material is collected, processed and manufactured, the less time trucks spend on the road transporting it, burning fuel and adding emissions to the atmosphere. It is estimated that more than 20 percent of the total cost of the materials used to build the new downtown campus come from building products that are extracted, processed or manufactured
Renewable Green Power: Plans call for purchasing Renewable Energy Certificates to offset more than 30 percent of the electrical power for Gateway’s new campus, thereby reducing the power purchased from traditional fossil fuel power plants and, hopefully, the adverse effects they can have on the environment.
Roof Garden: The new campus helps reduce the heat island effect (for definition, see “Reflective ‘Cool’ Roof” entry) in New Haven by featuring a roof garden with grass, trees and other plants, assisting in the reflection of heat. The roof garden is located on top of the fourth floor in the South Building, at the corner of Church and North Frontage Road on the top of the atrium and above the “radius” that has become the icon for the new campus and is home to the Library and Learning Commons.
Site Selection: This LEED strategy ensures that the project site is not inhabited by threatened or endangered animals, not previously used as farmland, and not on undeveloped land within 50 feet of a source of water that could adversely affect wildlife or fishing activities, and other issues that could hurt the surrounding natural environment. Gateway’s new campus meets all of these criteria.
Solar Hot Water System: The new campus uses two forms of solar energy. There are solar panels on the North Building to heat hot water and photovoltaic panels along the top of the entire Atrium section of the complex. Both provide the campus with self-generated energy that reduces utility costs. The 40 solar panels installed on the North Building heat two 500-gallon hot water tanks located in the basement of the building. Two-inch circulation pipes run from the boilers up to the panels, around the panels and back down to the boilers with the heated water.
Solar Shading and High-Performance Glazing: The shading and glazing for the windows and exterior glass “curtain wall” on the new downtown campus are designed to maximize indirect daylight penetration and minimize solar heat gain and glare.
Water-Efficient Fixtures and Landscaping: Gateway’s new campus is designed to use 40 percent less water when compared with a baseline campus. In order to maximize water efficiency and reduce the burden on the municipal water system, the campus features water-efficient fixtures, including waterless urinals, low flow-rate and flush fixtures, and sensor-activated fixtures. It also features water-efficient landscaping that reduces water usage in irrigation by 50 percent on the roof garden on the South Building, the outdoor garden outside the Community Center in the North Building, and the planters in front of the parking garage on Crown Street.